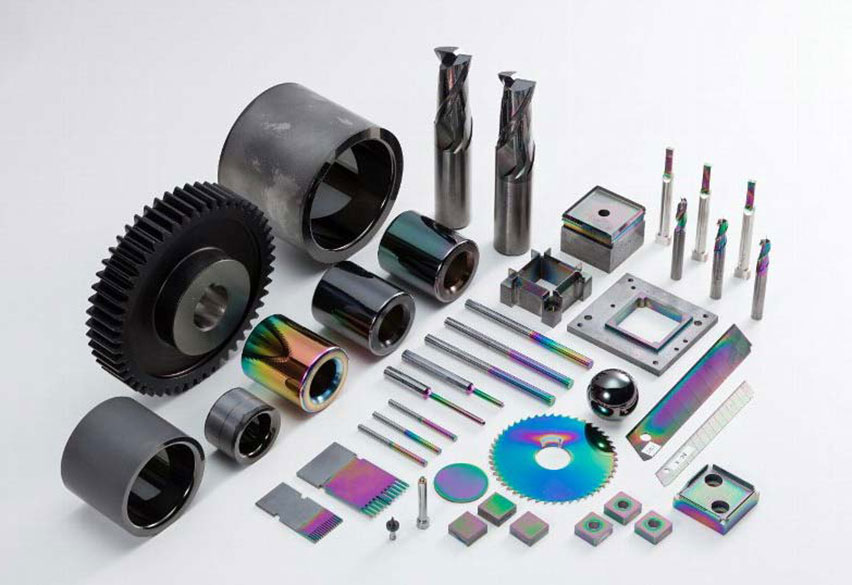
DLCは〈Diamond Like Carbon〉の略で、炭素(カーボン)を主体とした薄膜を、金属の表面などにコーティングする表面処理技術です。
ダイヤモンドとグラファイトなどの構造が混在するDLCは、チタン系やクロム系などの一般的なセラミックコーティングと比べ、硬くて滑りがよく、「耐摩耗性」「非鉄金属の耐凝着性」などの特性に優れています。
DLCの発見は、1971年まで遡ります。当時、メタンガスからダイヤモンドを合成する実験中に偶然発見された「黒くて硬い膜」は、その後DLCと名付けられ研究が進められてきました。
今では、切削工具・金型をはじめ、自動車部品や機械部品、医療部品など、ものづくりを支えるコーティングとして、幅広い業界で採用されています。
代表的なコーティング膜
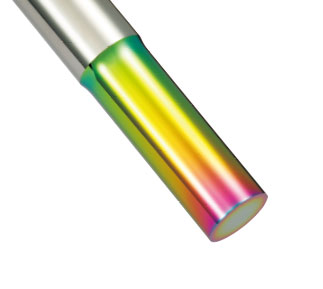
DLC
硬くて滑りがよく、様々な特性に優れます
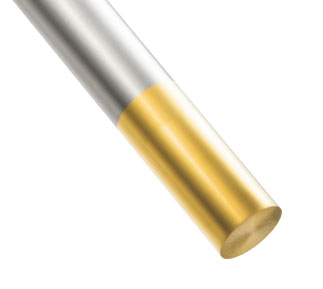
チタン系
主に切削工具や金型のコーティングとして使われています
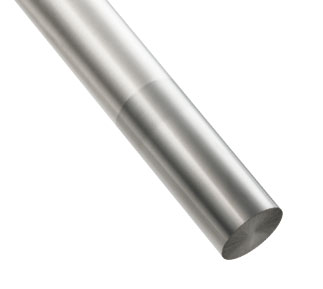
クロム系
主に金型や機械部品のコーティングとして使われています
DLCはSDGs?
DLCコーティングの特徴Feature
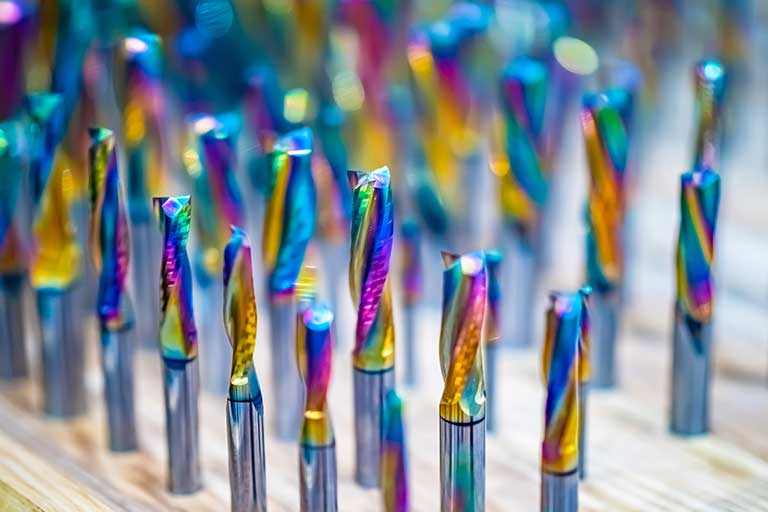
DLCコーティングの一番の特徴は、
「数ミクロンの膜厚」
「硬さのバリエーションがある(1000~7000Hv)」
「滑りのよさに優れる」点です。
DLCコーティングの主な特徴
- 高硬度
- 炭素の結びつき方で、7000Hv(AC-X)の高硬度もできる(ダイヤモンドは10000Hv)
- 低摩擦係数
- 全体が非晶質(ガラスのような構造)で、摺動性・平滑性に優れる
- 耐凝着性
- 炭素が主体のため、非鉄金属との非親和性に優れており、凝着や溶着・焼付きを起こしにくい
- 低相手攻撃性
- 低硬度DLCは、摩擦時に発生する相手材料のキズや摩耗が少ない傾向にある
- 耐食性
- 化学的に不活性のため、さびに強く、腐食しやすい雰囲気でも劣化しにくい
- 電気特性
- グラファイト構造やダイヤモンド構造の比率、水素、金属の含有量によって、導電傾向や絶縁傾向になる
- 生体親和性
- 炭素を原料としているため、人体への影響が少ない
DLCコーティングは、上記以外にも、ガスバリア性(ガスの遮断)や、光学特性(赤外線の透過や紫外線の遮断)、撥水性・耐薬品性・抗菌性など、様々な特徴を持っています。
DLCコーティングの特性とセラミックコーティングとの比較
一般的なセラミックコーティングとの比較は下記の通りです。
特徴 | DLCコーティング (ta-Cタイプ)※2 |
DLCコーティング (a-C:Hタイプ)※2 |
セラミックコーティング | |
---|---|---|---|---|
膜種※1 | AC-X | DLC-EX | TiN | CrN |
硬度 | 7000Hv | 3000Hv | 2200Hv | 1700Hv |
膜厚 | ~0.5μm | ~1.0μm | 2~4μm | 2~4μm |
耐酸化温度 | 550℃ | 400℃ | 500℃ | 700℃ |
処理温度 | 100〜150℃ | 200~250℃ | 400〜500℃ | 400〜500℃ |
摩擦係数 | 0.09~0.13 | 0.09~0.13 | 0.55 | 0.45 |
構造 | 非晶質 | 非晶質 | 結晶 | 結晶 |
※2. ta-Cタイプおよびa-C:Hタイプについてはこちら
切削工具におけるDLCの向き・不向き、アルミと鉄
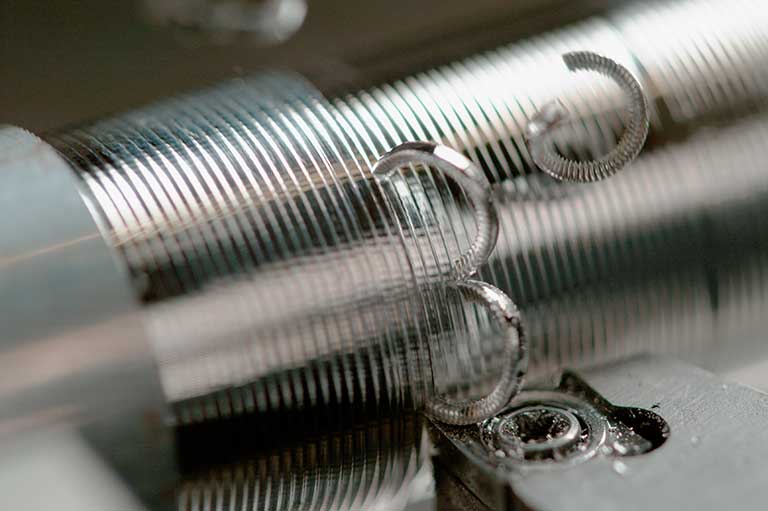
様々な特性を持つDLCコーティングですが、一般的なダイヤモンド工具と同じく、鉄系材料の切削には向いていません。鉄と炭素は親和性が高く、加工時に発生する熱でコーティングが軟化(スス化)してしまうのが原因です。
一方、DLCコーティングは軟質の純アルミや銅、アルミ合金、アルミダイカスト(ADC)などの非鉄金属加工時の凝着・溶着を抑えることが期待できます。
凝着とは?
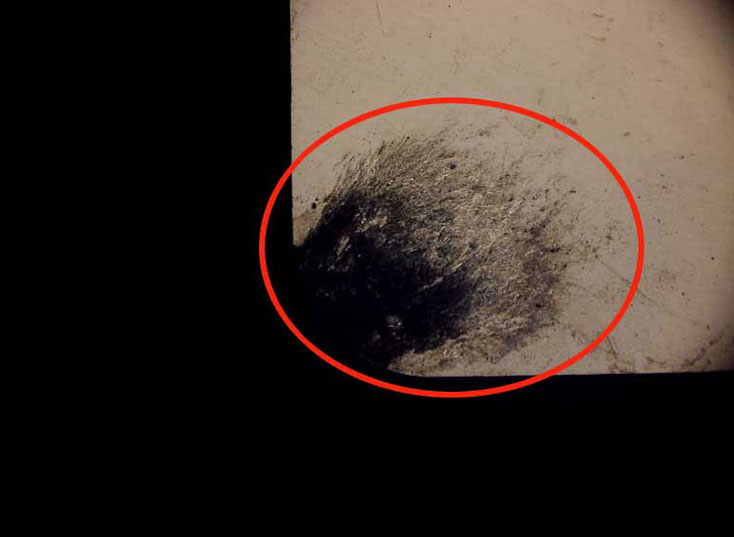
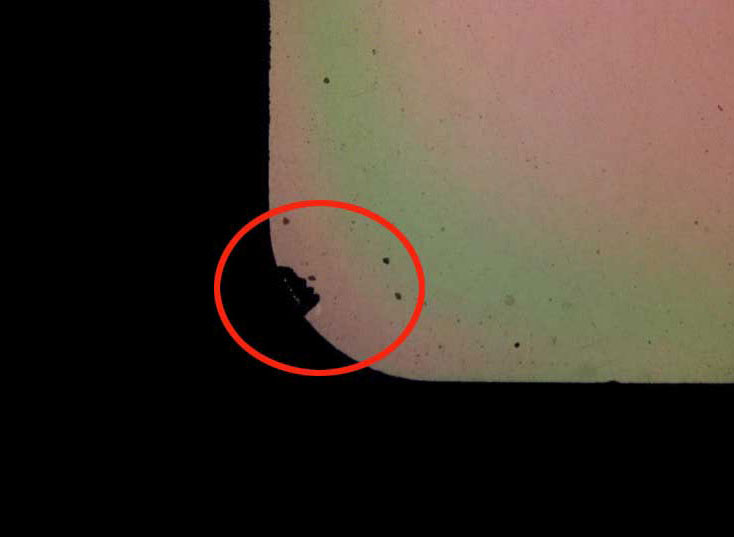
DLCコーティングにも欠点がある?
ダイヤモンドに近い硬度のDLCもありますが、一方で、硬質で非晶質のため母材変形への追従性が低く、衝撃でクラックが入ってしまうと、ガラスにひびが入るように伝播してしまうことがあります。
また切削工具や金型へコーティングする場合、一般的なダイヤモンド工具と同じように、鉄系材料の切削には向いていません。
DLCコーティングは、母材の材質や表面状態、使用環境に敏感です。「硬さ」だけではなく、耐酸化温度や、相手材との非親和性を考慮しなければ、せっかくのコーティングも活かすことができません。
オンワード技研では、お客様の用途や課題に合わせて、最適なDLCコーティングをご提案いたします。
DLCに関するご相談は、ぜひ一度、お問い合わせください。
DLCコーティングの用途例Application
DLCコーティングは、その「硬さ」と「滑りのよさ」から、切削工具・金型だけでなく、自動車部品や機械部品、医療部品など、様々な業界で幅広く採用されています。
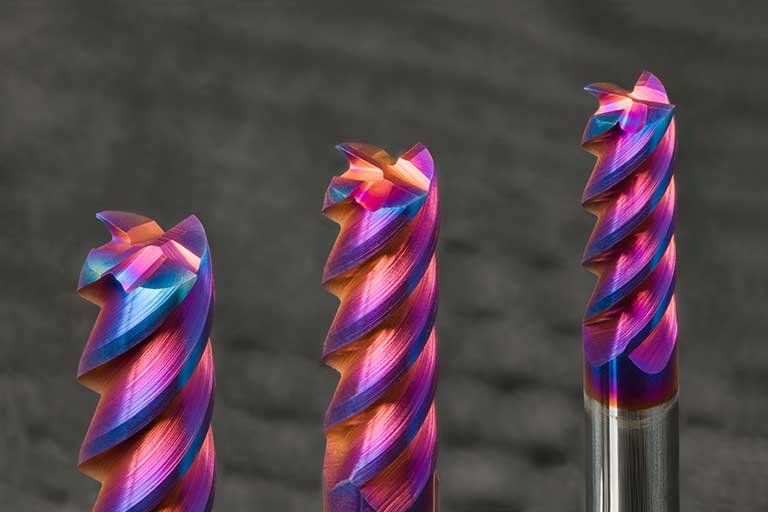
切削工具におけるDLCコーティングの例
切削工具では、主に摩耗防止・長寿命化を目的に、DLCコーティングが採用されています。耐凝着性を利用して、アルミ加工やドライ加工用の切削工具にも使われています。
また摩擦による切削熱を抑えることができるため、工作機械本来の高い加工精度を発揮することができます。
- コーティングの例
- エンドミル、フライス工具、ドリル、バイト、リーマ、切断刃、メタルソーなど
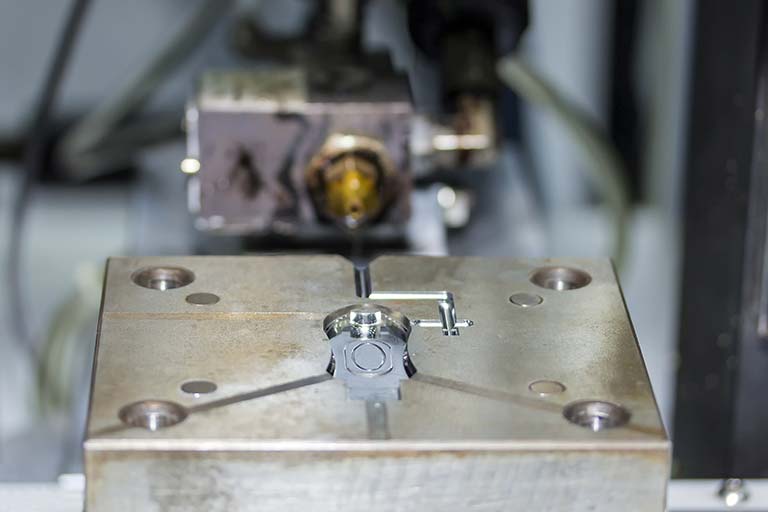
金型におけるDLCコーティングの例
金型では、主に摩耗防止・長寿命化を目的に、DLCコーティングが採用されています。DLCコーティングは、他のコーティングと比べ低温成膜で薄膜のため、金型の精度に影響しにくいです。
また溶融ガラスの離型性向上にも使われています。
- コーティングの例
- プレス金型、レンズ金型
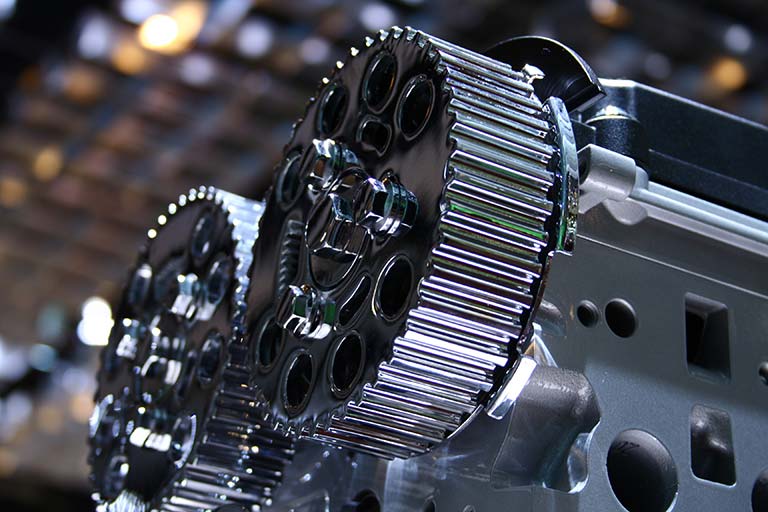
自動車部品におけるDLCコーティングの例
自動車部品では、主に摺動特性を生かした耐摩耗性の向上を目的に、DLCコーティングが採用されています。エンジンケース内の過酷な環境下でも、高い耐久性と低相手攻撃性で、部品の破損を防ぎ、安全性向上に貢献します。
また摩擦抵抗が少なく、エネルギーロスを減らすことができ、燃費向上やCO2排出量の削減にもつながります。
- コーティングの例
- エンジン部品、トランスミッション部品、ギア、駆動部品、外装・内装部品など
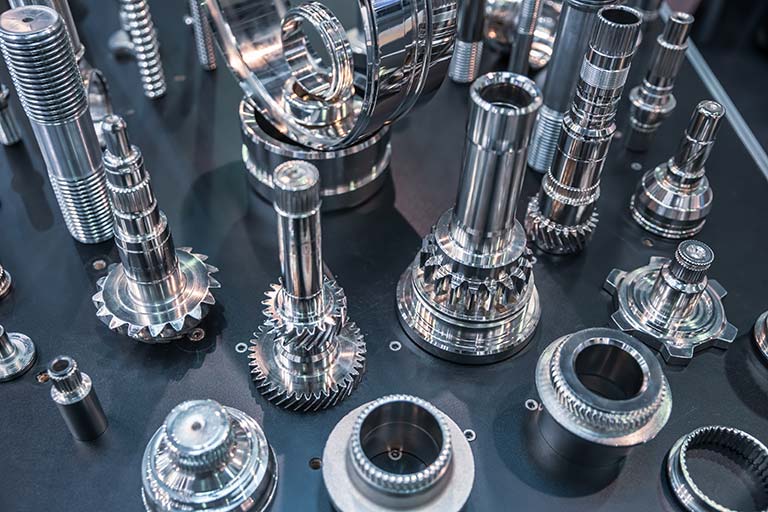
機械部品におけるDLCコーティングの例
ギアやプーリー、シャフト、軸受などの機械部品では、摺動性と耐久性向上を目的に、DLCコーティングが採用されています。また平滑性が求められるハードディスクなどの電子部品や、筐体のキズ・汚れの防止にも使われています。
DLCは摩耗による発塵が少ないため、半導体製造装置やクリーンルームでの使用にも適しています。
- コーティングの例
- 機械要素部品、伝動部品、軸受部品、電子部品、半導体製造装置部品など
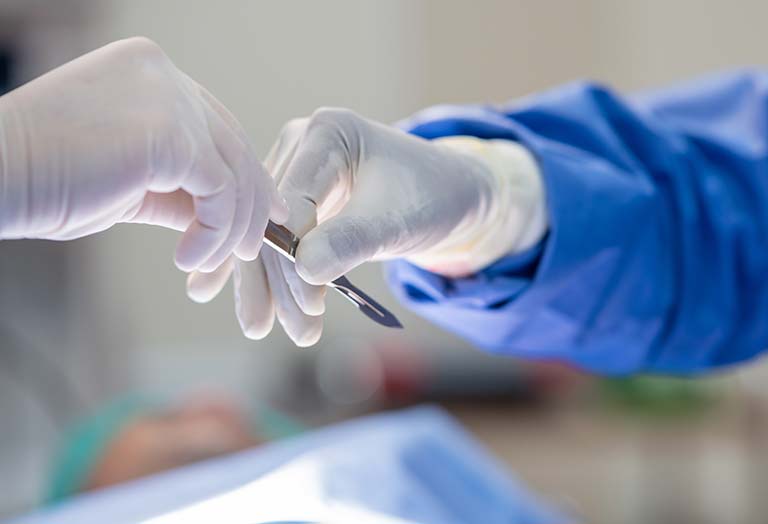
医療業界におけるDLCコーティングの例
DLCコーティングは生体親和性が高く、医療器具や手術用具、医療用材料、インプラント、ステントなどへの応用が進んでいます。
体内への挿入をスムーズにするだけでなく、高い耐薬品性や抗菌性で、患者の負担を和らげることができます。
- コーティングの例
- ピンセット、メス、注射針、人工関節、インプラント、ステントなどなど
身近なモノにも使われています!
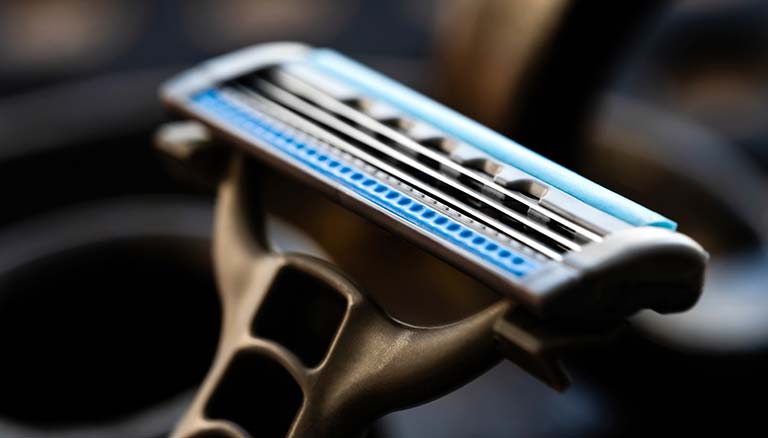
そもそもDLCとは?ダイヤモンドとグラファイトの特徴Diamond & Graphite
DLCは、ダイヤモンド結合(sp3)とグラファイト結合(sp2)が混在した、アモルファス構造(非晶質構造)と呼ばれる物質です。sp3とsp2の比率によって、硬さと滑りの特性が異なります。
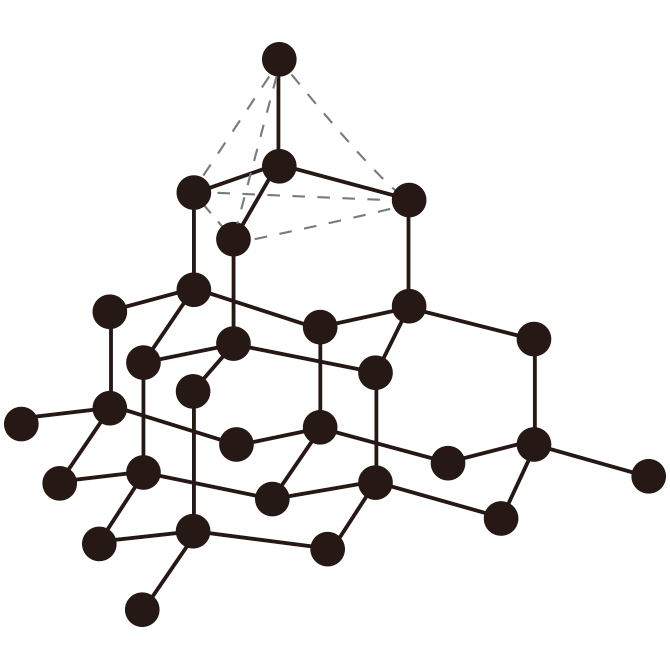
(炭素の正四面体立体構造)
自然界で最も硬い物質。原子同士の結合が強く、高い熱伝導率や絶縁性などの性質を持っています
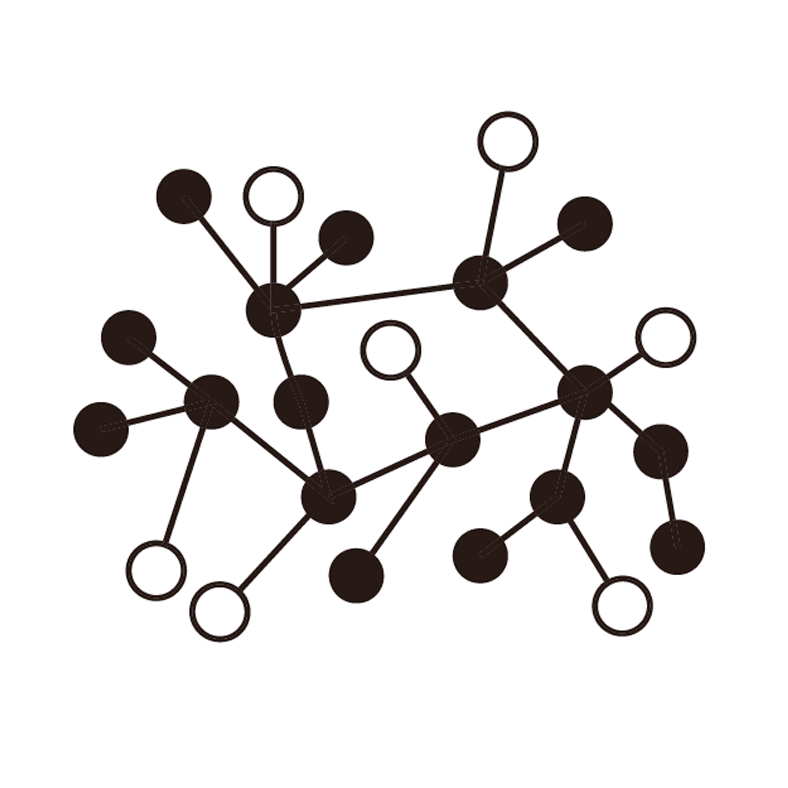
(アモルファス構造)
ガラスのような非晶質(アモルファス構造)で、非連続のsp3、sp2が混在して独自の特性を持ちます
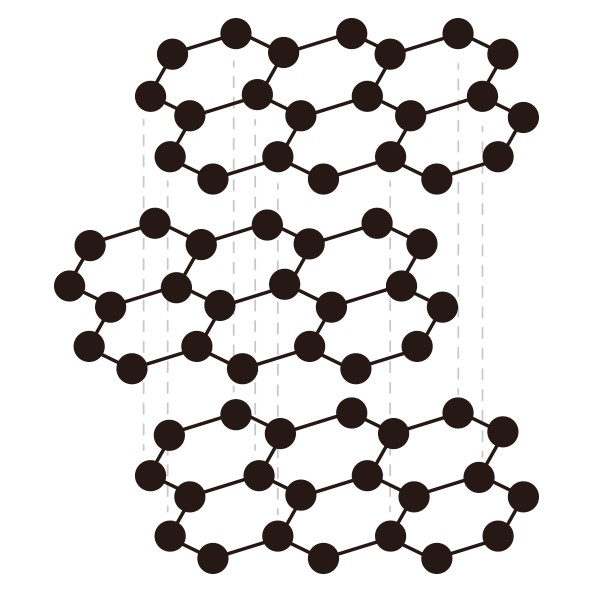
(六角状の積層構造)
各層間の結合が弱く、これがずれることで、滑り性が向上します。
DLCの種類と特徴
DLCは、さらに「水素」を添加することで、膜の特性を変化させることができます。 その種類は、ダイヤモンド・グラファイトの比率と、水素(H)の有無によって、大きく4つに分けられます。
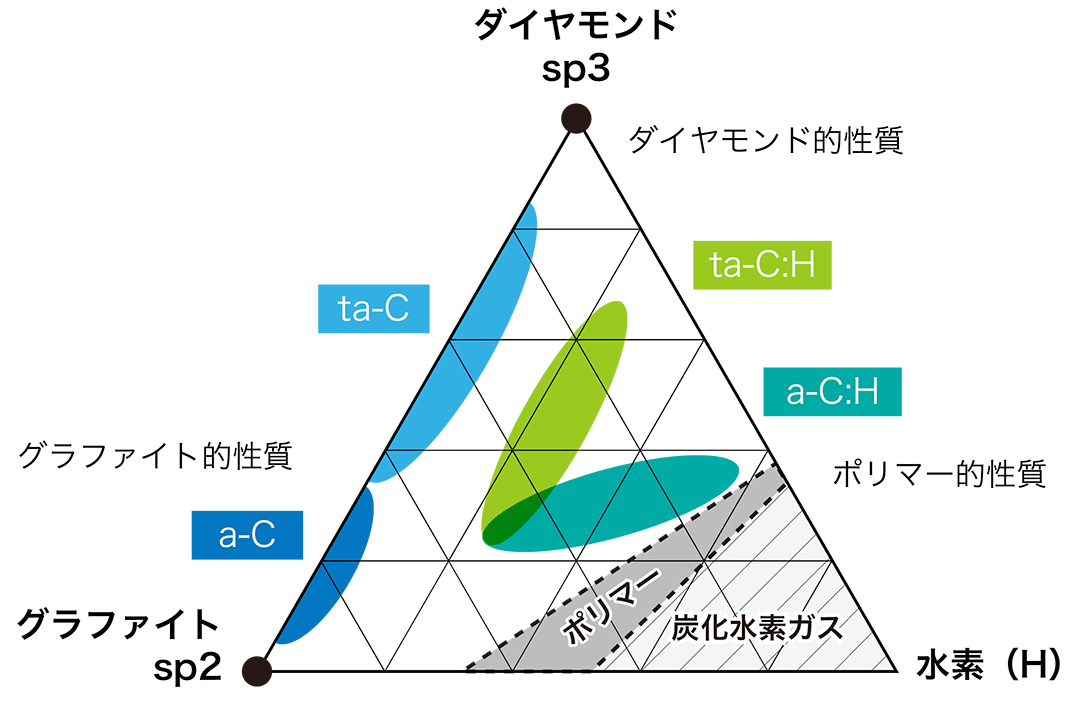
タイプ | 水素の有無 | sp2とsp3の比率 | |
---|---|---|---|
ta-C | テトラヘドラルアモルファスカーボン | なし(水素フリー) | sp3の比率が大きい |
a-C | アモルファスカーボン | なし(水素フリー) | sp2の比率が大きい |
ta-C:H | 水素含有テトラへドラルアモルファスカーボン | あり(水素含有) | sp3の比率が大きい |
a-C:H | 水素含有アモルファスカーボン | あり(水素含有) | sp2の比率が大きい |
DLCコーティングの色合いについて
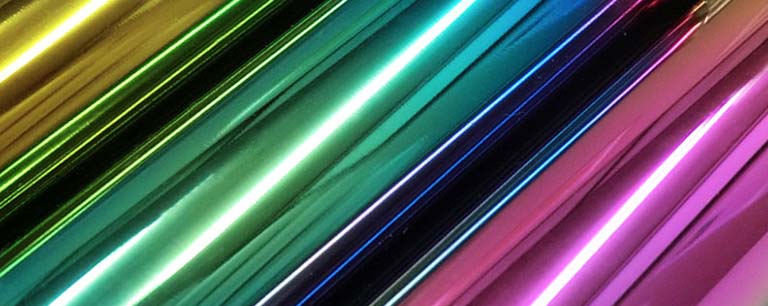
近年では、その外観の美しさと高い耐久性から、腕時計やルアー、自転車部品、ゴルフクラブなど、日用品への応用も広がっています。
DLCの選び方
工具や薄板打ち抜きパンチへの適用は、硬さを活かした用途が多いため、ダイヤモンド(sp3構造)の比率が高い「ta-C」が主流となっています。
一方で部品への適用は、硬度は落ちるがじん性と密着強度が優れる、「a-C:H」がおすすめです。
オンワード技研では、お客様の用途や課題に合わせて、最適なDLCコーティングをご提案いたします。
DLCに関するご相談は、ぜひ一度、お問い合わせください。
DLCコーティングと成膜方法Production
DLCの成膜には、PVD(物理蒸着)や、CVD(化学蒸着)などの技術が用いられます。
ここでは、オンワード技研にて行っている「イオン源蒸着」「PCVD」「FAD」について説明します。
イオン源蒸着
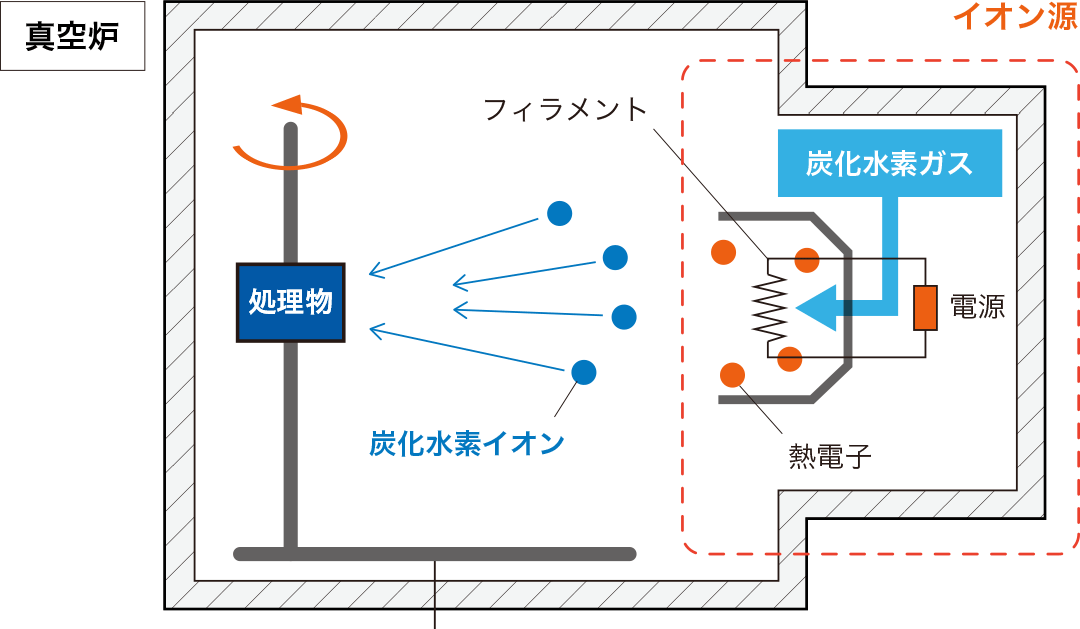
フィラメントを加熱し、熱電子により炭化水素ガスをイオン化させ、電位差をつけた処理物に衝突させてコーティングする、PVDの一種です。
炭化水素ガスを原料とするため、水素含有DLCとなります。汎用性が高く、ザラツキのないきれいな表面が得られるため、広く使われています。
PVDとは?
電位差を用いることで、衝突エネルギーが増大し、単なる蒸着と比べ強固な膜を生成できます。
PCVD(プラズマ化学蒸着)
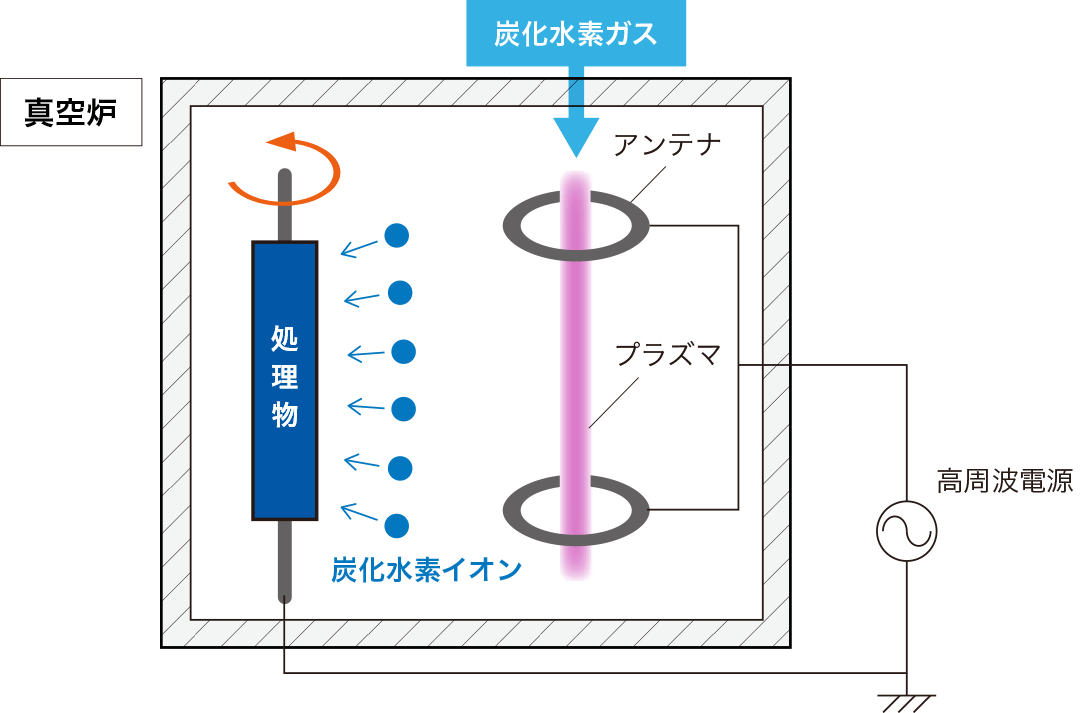
PCVDは、プラズマ領域でイオン化させた炭化水素ガスを、電位差をつけた処理物に衝突させて、コーティングします。PCVD(プラズマ化学蒸着:Plasma Chemical Vapor Deposition)の一種です。
真空炉内に設けられたループアンテナに高周波電流を流すことで、広範囲にプラズマを発生するため、長尺品も均一に成膜することができます。
オンワード技研では、自社製作炉によって、他社では難しい1m程度の長尺ワークにも成膜が可能です。
FAD(フィルタードアーク蒸着)
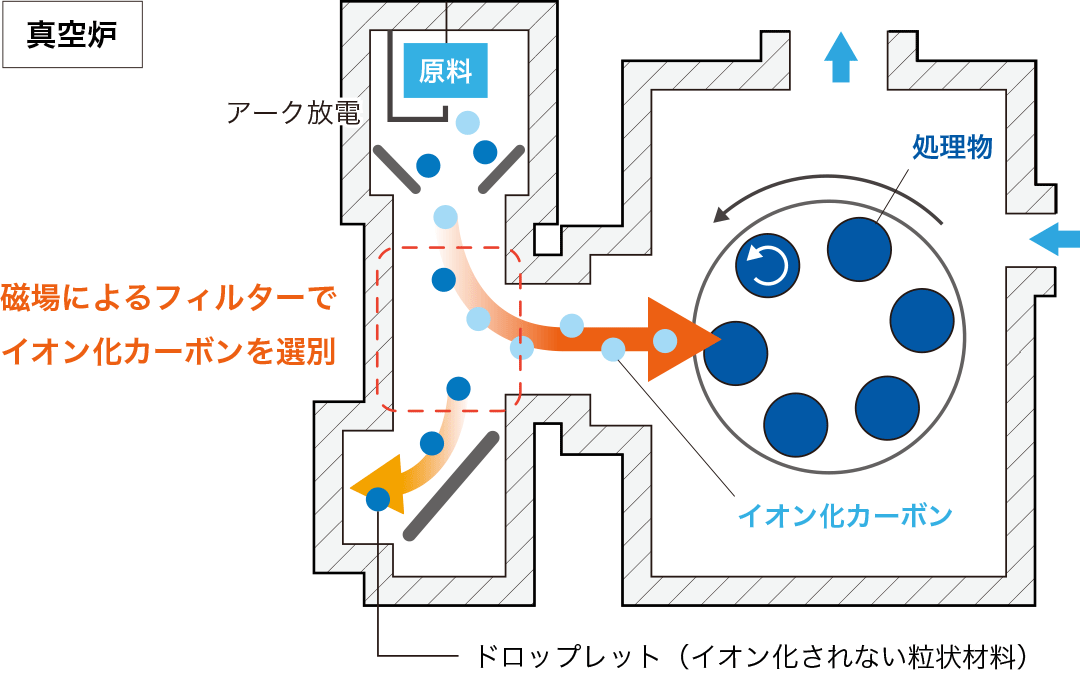
FADは、アークイオンプレーティングの欠点である「ドロップレット(膜中に混入するイオン化されない粒状材料)」を減らし、強固できれいな膜を得ることができます。
FADでは、磁場によるフィルターでイオン化されたカーボンのみを処理物に引き込み、成膜します。ダイヤモンド(sp3構造)の比率が高い水素フリーDLCが得られます。
DLCコーティングにおけるオンワード技研の強みONWARD GIKEN
オンワード技研では、1986年、東ドイツからのDLC試験機導入を皮切りに、「量産に使えるDLCコーティング」の研究開発に着手。DLCのパイオニアとして、国内でいち早くDLCコーティングを事業化しました。

その後、大学や公設試など研究機関との共同研究にも取り組みながら、数多くの特許を取得。コーティング装置を内製化することで、より安定した生産と、さらなるノウハウの蓄積に取り組んでいます。
現在では高い技術力と提案力が評価され、全国802社以上と直接取引。特に金型のDLCコーティングでは国内トップシェアを占めるなど、日本のものづくりに貢献しています。
- 2002年・2008年
- 石川県「石川ブランド」認定
- 2007年
- 経済産業省「元気なモノ作り中小企業300社」認定
- 2018年
- 経済産業省「地域未来牽引企業」認定
クリーンルーム完備で、高品質のDLCに対応
オンワード技研では、業界では珍しいクラス10,000(ISOクラス7)のクリーンルームを完備。半導体向けの精密金型など、高い品質が求められるDLCコーティングを強みとしています。
また2021年には「医療機器製造業許可」を取得。医療分野向けのDLCコーティングも、安心してお任せいただけます。
オンワード技研のDLCコーティングの流れFlow
オンワード技研が得意とするDLCコーティングは、大量生産ではなく、少量多品種生産です。
お客様からお預かりした多種多様な製品を、一品ずつ丁寧に検品・前処理をしながら成膜を行っています。また各工程では全数検査を行い、品質管理を徹底するなど、手作業でしかできないきめ細やかな対応で、高品質なコーティングを提供しています。
- Flow.01
- 入荷検査
- お客様からお預かりした製品を検査し、コーティング可能な表面状態かを入念に確認します。
- Flow.02
- 前処理(手磨き・洗浄)
- 入荷検査の状態に合わせて、手磨きやラップ処理・洗浄を行い、成膜後の剥離リスクを減らします。※3
- Flow.03
- 成膜工程
- 前処理が終わったら、コーティング室へ移り、真空炉によってコーティングを行います。 成膜方法には、成膜装置・膜種によって「イオン源蒸着」「PCVD」「FAD」などがあります。
自社開発した装置と最適なコーティング条件により、高品質なDLCを提供いたします。
- Flow.04
- 検査・出荷
- 成膜後は全数検査を行い、出荷します。
※3.DLCコーティングの剥がれについて
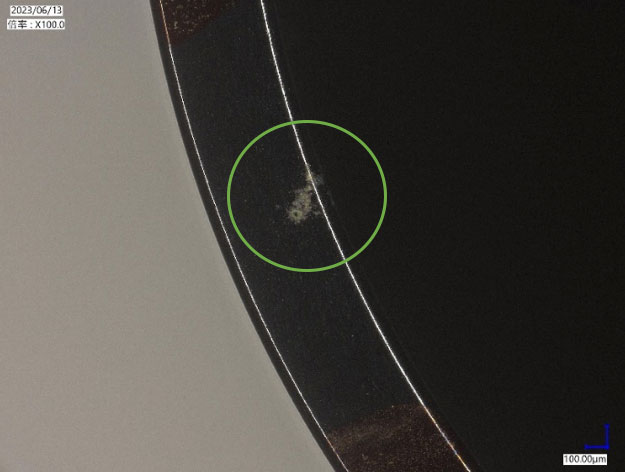
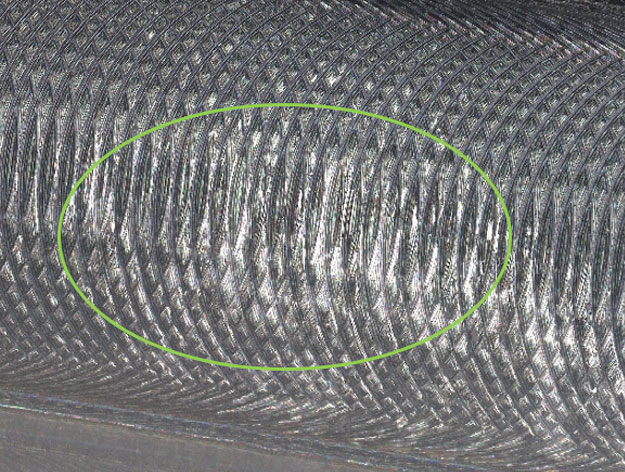
オンワード技研のDLCコーティングラインナップProduct Lineup
オンワード技研では、お客様の用途や課題に合わせた各種DLCをご用意しています。
それぞれ膜厚や硬度に特徴がありますが、一般的なDLCコーティングのご要望については、まずは「DLC-EX」と「AC-X」で対応が基本です。まずはこの2種からお試しください。
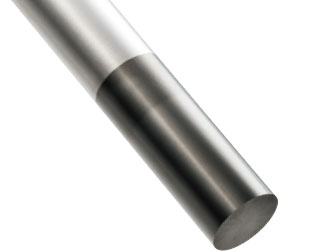
DLC-EX
a-C:Hタイプの水素含有DLC。Si系のアンダーコートでコーティング可能な母材の選択肢も広く、汎用的なDLCコーティングとして使われています。
DLC-EXをベースに、薄膜の「DLC Prism」、撥水仕様の「CFC-H」、耐熱仕様の「XPC」などのラインナップをご用意しています。
DLC-EXの詳細はこちら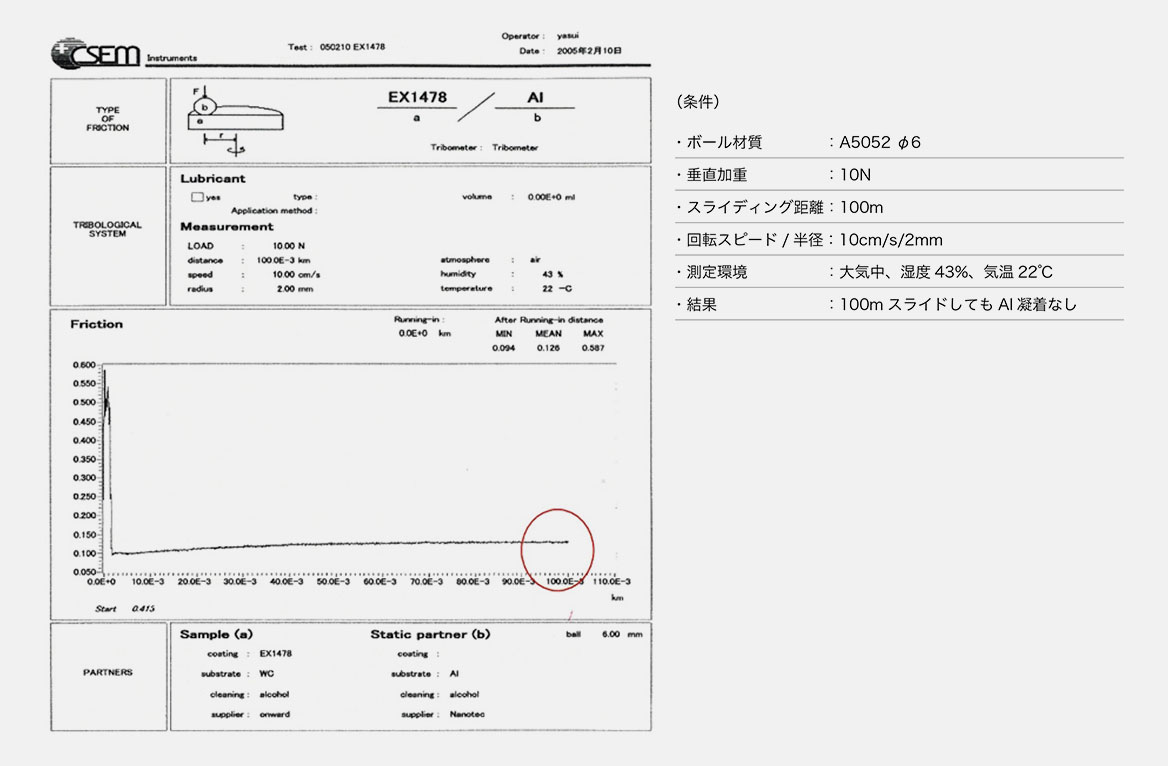
DLC-EXを成膜した超硬テストピースに、アルミニウムのボールを押し付け100mスライドさせても凝着がありません
( クリックで拡大)
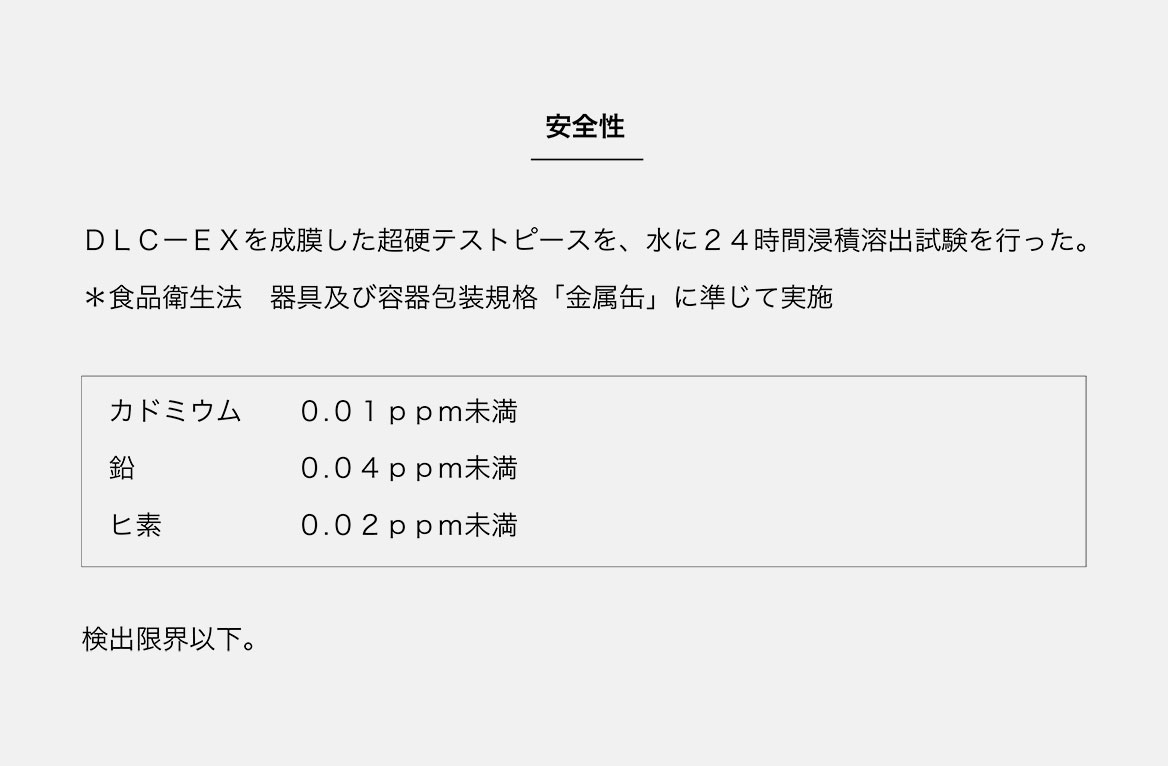
DLC-EXを成膜したワークを水に24時間浸しても、上記の成分の溶出がありません
(クリックで拡大)
- DLC-EX 用途例
- アルミ切削工具、摺動部品、半導体製造装置部品、樹脂トリミング工具など
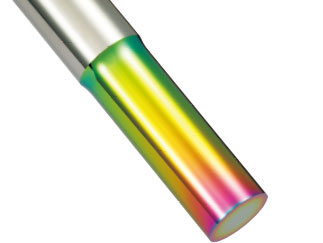
AC-X
ta-Cタイプの水素フリーDLC。DLC-EXよりもさらに硬度が高く、耐酸化温度も向上しています。
AC-Xをベースに、厚膜の「AC-X・W」、硬度を落としじん性を上げた「AC-X・X」などのラインナップをご用意しています。
AC-Xの詳細はこちら〈AC-Xの切削試験データ〉
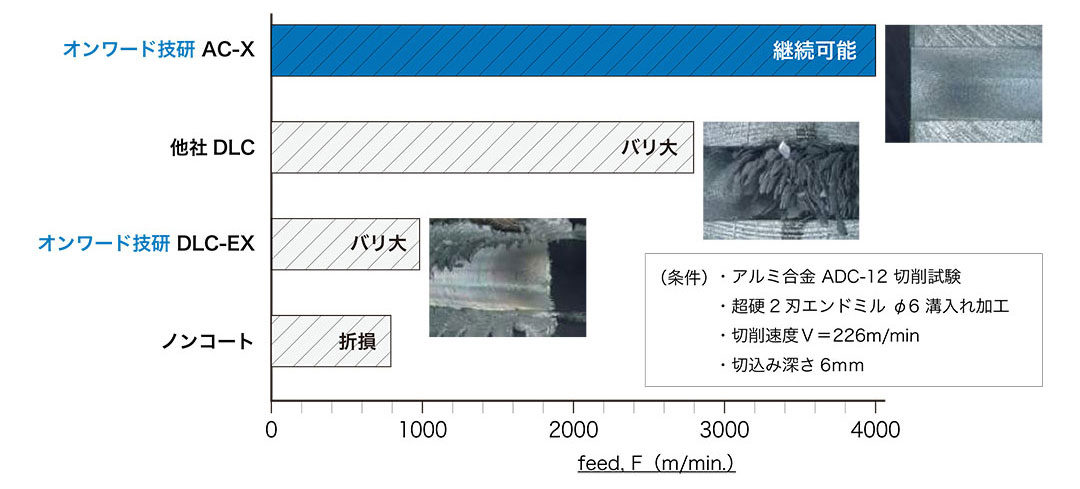
AC-Xを成膜した工具は、ADC-12の加工において、DLC-EXと比較して2倍以上の継続切削が可能です(クリックで拡大)
- AC-X 用途例
- 超硬工具、プレス金型、超硬パンチ、リードフレーム加工型、樹脂成型、耐摩耗部品など
DLCコーティングのよくあるご質問FAQ
-
DLCコーティングの選定・依頼方法は?
まずはお電話・メールなどでお打ち合わせを依頼いただき、大きさ・母材材質・用途などから膜の選定を行います。図面を提示いただければ、よりスムーズにお打ち合わせが可能です。
-
一個からでも大丈夫?
はい。当社では、少量多品種をメインに受託しており、大きさで生産機が限定される場合を除き、基本一個から受注生産に対応しています。
-
サンプル加工はできる?
サンプル加工には、基本的には対応しておりません。
-
コーティングできない場合はある?
成膜時の熱によって変寸・変質してしまう材質や、組み込み品、メッキ品、処理炉に入らない大きなものなどは、コーティングができない場合もあります。お打ち合わせの際にご説明いたします。
DLCコーティングなら、オンワード技研にご相談ください
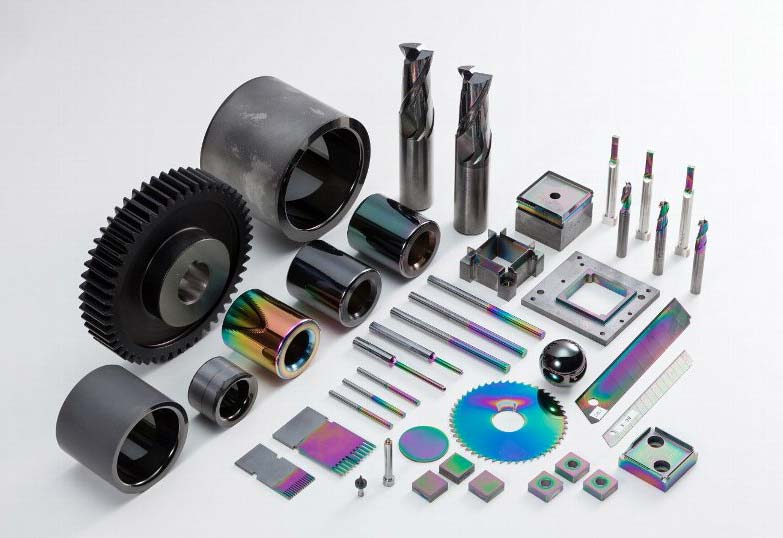
DLCコーティングは、成膜装置や成膜条件によって各メーカーの個性が強く、「どこのメーカーのDLCも同じ」というわけではありません。ダイヤモンドの合成実験で偶然発見されたDLCは、未だに学会でも研究が続けられており、量産で使えるDLCの成膜には、高い技術が必要とされています。
そのような中、当社では1986年のDLCコーティング装置導入以来、「生産に使えるDLCコーティングメーカー」として、多くの実績を積んできました。
このようお困りではありませんか?
- 他社でDLCコーティングをしたが、上手くいかない…
- スペックが高い膜なのに、どうしても性能がでない…
- 用途が合わず、コーティングが剥がれてしまった…
- 使いこなすのが難しそう…
DLCに関するご相談は、ぜひ一度、オンワード技研までお問い合わせください。
お客様の用途や課題に合わせて、最適なDLCコーティングをご提案させて頂きます。
DLCコーティングは「万能の膜」ではありません
お客様がDLCコーティングを使いこなせるよう、当社がお力になれれば幸いです